CONTRÔLE QUALITÉ FONTE
INTRODUCTION
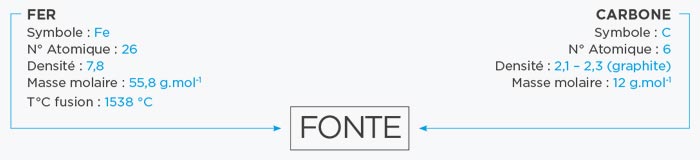
L’élaboration de la fonte commence par le minerai de fer qui est introduit dans un haut fourneau ainsi que du coke (carbone). Le fer sera extrait du minerai par réduction. Cette fonte est appelée fonte de première fusion. Elle peut être utilisée telle quelle pour certaines applications, ou pour l’élaboration de l’acier.
Une seconde méthode existe pour élaborer la fonte : à partir de ferrailles d’acier et de coke. Différents procédés existent : le cubilot, des fours électriques ou encore des fours rotatifs.
Fig 1 : Schéma d’un haut fourneau
• Les fontes hypoeutectique avec moins de 4,3 % de carbone
• Les fontes eutectiques avec 4,3 % de carbone
• Les fontes hypereutectoïdes avec plus de 4,3 % de carbone
Le diagramme d’équilibre Fe-C (figure 2) permet d’expliquer la solidification depuis l’état liquide.
Fig. 2 : Diagramme Fe-C
LES PRINCIPALES FONTES
LES FONTES BLANCHES
Le carbone se trouve sous forme de carbure Fe3C et une matrice perlitique. Son nom vient du fait que lors d’une casse, son aspect est métallique blanc brillant. La fonte blanche est une fonte alliée avec du manganèse. Les présences de chrome et de molybdène vont également favoriser la création de fonte blanche. Ce type de fonte est résistant à l’usure mais est fragile aux chocs.
LES FONTES GRISES
Le carbone apparaît sous forme de graphite (sphéroïdal ou lamellaire). Ces fontes sont riches en silicium, cet élément d’addition favorise la formation du graphite. Il permet également d’améliorer la résistance à la corrosion.
=> Les fontes à graphite lamellaire sont fragiles du fait de la géométrie du graphite qui a un effet d’entaille. La résistance à la traction n’est pas optimale mais pour des applications de travail en compression ou pour un besoin de résistance à l’usure, celle-ci sera adaptée.
=> Les fontes à graphite sphéroïdal sont des fontes où le refroidissement a été ralenti pour que le carbone cristallise sous forme de sphère. La géométrie du graphite permet d’améliorer l’usinabilité et les caractéristiques mécaniques s’approchent de celles d’un acier. C’est une fonte ductile, malléable. L’ajout de magnésium dans la fonte va diminuer la présence de soufre. Ainsi le graphite va se former de manière sphérique et non en lamelle. Il est possible de créer une fonte à graphite sphéroïdal à partir d’une fonte blanche qui subit un traitement thermique.
Dans les fontes alliées :
• Le chrome augmente les caractéristiques mécaniques
• Le molybdène améliore la résistance aux chocs
• Le phosphore permet à la fonte d’avoir une meilleure coulabilité
La composition chimique du mélange est un des paramètres qui va déterminer le type de fonte obtenu.
La vitesse de refroidissement influe sur la formation de l’une ou l’autre des fontes.
• Si la vitesse de refroidissement est rapide : cela favorise la formation de cémentite, et donc l’obtention d’une fonte blanche.
• Si la vitesse de refroidissement est lente : le carbone a le temps de se rassembler sous forme de graphite et cela correspond donc à une fonte grise.
DÉSIGNATION DES FONTES
Leur désignation commence toujours par EN-GJ (G correspond à un métal moulé et J pour le fer). Une autre lettre qui correspond à la structure du graphite suit ce début de désignation :
L pour Lamellaire
S pour Sphéroïdale
M pour graphite de recuit (malléable)
V pour vermiculaire
Y pour structure spéciale
N pour absence de graphite
Généralement, tout ceci est suivi soit de la résistance minimale à la rupture et de l’allongement mini- mal exigé en % ou soit de la même désignation qu’un acier fortement allié.
Voici deux exemples :
EN-GJS-400-15 : Fonte à graphite lamellaire, résistance R min 400 MPa et allongement A 15%
EN-GJN-X 300 Cr Ni Si 9-5-2 : Fonte sans graphite (fonte blanche) à 3% de carbone, 9% de chrome, 5 % de nickel et 2% de silicium
=> Il existe de nombreuses nuances de fonte afin de répondre à toutes les applications selon les pro- priétés de résistance aux chocs, résistance à l’usure et de bonne coulabilité…
APPLICATIONS
PRÉPARATION MÉTALLOGRAPHIQUE
• La standardisation de la géométrie de l’échantillon prélevé (si nécessaire), appelée « ENROBAGE ».
• L’amélioration de l’état de surface de cet échantillon, appelée « POLISSAGE ».
• La caractérisation de l’échantillon : révélation de la microstructure de l’échantillon par un réactif d’attaque (si nécessaire) appelée « ATTAQUE MÉTALLOGRAPHIQUE » et l’observation microscopique (optique ou électronique).
TRONÇONNAGE
En d’autres termes il est indispensable d’éviter un échauffement ou une déformation des fontes pouvant entraîner des modifications de structure. Le tronçonnage est une étape fondamentale qui conditionne la suite de la préparation et l’observation des pièces.
La large gamme de micro-tronçonneuses et tronçonneuses de moyenne et grande capacité PRESI permet de s’adapter à n’importe quel besoin en termes de précision de découpe, de dimensionnement ou de quantité de produits à découper :
CONSOMMABLES
FONTES GRISES | FONTES BLANCHES | |
Micro-tronçonnage | S (Ø 180mm) UTW |
S (Ø 180mm) AO CBN |
Tronçonnage de moyenne capacité | F MNF AO |
F AO CBN |
Tronçonnage de grande capacité | MNF AO |
AO |
Tableau 1 : Choix du type de meule de tronçonnage adapté
ENROBAGE
Réaliser un enrobage de qualité est essentiel afin de protéger les matériaux fragiles mais également pour obtenir de bons résultats de préparation en vue du polissage et des futures analyses.
Avant toute opération d’enrobage, l’échantillon doit être ébavuré à l’aide par exemple, d’un papier abrasif (pour éliminer les éventuelles bavures de coupe) suivi d’un nettoyage à l’éthanol. Cette opération permet à la résine d’adhérer au mieux sur l’échantillon et ainsi limiter le phénomène de retrait (gap entre la résine et l’échantillon).
Il existe deux procédés d’enrobages :
LE PROCÉDÉ À CHAUD
• Presse d’enrobage à chaud totalement automatique.
• Simple d’utilisation, la mémorisation, l’ajustement des procédés et la rapidité d’exécution en font une machine de haute précision.
• L’enrobeuse à chaud propose six moules de diamètres différents allant de Ø25,4mm à Ø50mm.
LE +
LE PROCÉDÉ À FROID
• Les pièces à examiner sont fragiles / sensibles à la pression
• Les pièces présentent une géométrie complexe (structure en nid d’abeille).
• Le besoin est d’enrober un grand nombre de pièces en série.
Le procédé à froid peut être utilisé avec :
LE +
LE +
CONSOMMABLES
FONTES GRISES ET BLANCHES |
|
A chaud | Phénolique Acrylique Epoxy |
A froid | KM-B KM-U |
Tableau 2 : Choix du type de résine d’enrobage
POLISSAGE
PRESI propose une grande gamme de polisseuses manuelles et automatiques, avec un large choix d’accessoires, afin de couvrir tous les besoins, du pré-polissage à la superfinition et du polissage d’échantillons unitaires ou en série.
La gamme de polisseuses automatiques MECATECH permet un polissage aussi bien manuel qu’automatique. Avec ses technologies avancées, ses puissances moteur de 750 à 1500 W, toute l’expérience de PRESI est concentrée dans cette gamme complète. Peu importe le nombre ou la taille des échantillons, MECATECH garantie un polissage optimal.
CONSOMMABLES ET GAMMES DE POLISSAGE
Toutes les premières étapes de chaque gamme sont appelées « mise à niveau » et consistent à retirer de la matière rapidement afin de mettre à niveau la surface de l’échantillon (et de la résine). Celles données ci-dessous sont standards et peuvent, par conséquent, être modifiées selon le besoin.
Les forces d’appui varient selon la taille des échantillons mais de manière générale il sera appliqué : 1daN par 10mm de diamètre d’enrobage pour les étapes de pré-polissage (ex : Ø40mm = 4 daN) puis la force sera diminuée de 0,5daN à chaque étape de polissage avec une suspension abrasive.
La gamme de polissage suivante est une gamme d’ordre général pour les fontes :
N° | Support | Suspension / Lubrifiant |
Vplateau (tr/min) |
Vtête (tr/min) |
Sens de rotation Plateau / tête |
Temps |
1 | P320 | Ø / Eau | 300 | 150 | 1’ | |
2 | TOP | 9μm ADS poly / Lub ADS | 150 | 135 | 4’ | |
3 | STA | 3μm ADS poly / Lub ADS | 150 | 135 | 3’ | |
4 | TFR | 1μm ADS poly / Lub ADS | 150 | 135 | 1’ |
Nota : La mise à niveau à l’aide du papier abrasif P320 est suffisante pour un échantillon provenant d’une coupe métallographique. Si un enlèvement de matière plus important est nécessaire, il faut utiliser un papier abrasif avec une granulométrie plus importante.
Lors du prépolissage, il n’est pas nécessaire d’inverser les sens de rotation de la tête et du plateau car cela peut détériorer la planéité. Cependant, l’inversion des sens de rotation peut aider si un enlèvement de matière important est à faire.
Le polissage de la fonte s’effectue généralement à l’aide de suspension diamantée polycristalline ADS (base alcool, exempt d’eau). Cela évite l’oxydation de la fonte qui est sensible à l’eau lors du polissage de finition.
Lors du nettoyage entre chaque étape, un séchage rapide à l’air comprimé après nettoyage à l’eau est conseillé, ou bien un nettoyage à l’éthanol va limiter l’apparition de point de corrosion.
N° | Support | Suspension / Lubrifiant |
Vplateau (tr/min) |
Vtête (tr/min) |
Sens de rotation Plateau / tête |
Temps |
1 | I-Max R 54μm | Ø / Eau | 300 | 150 | 3’ | |
2 | MED-R | 9μm super abrasif MED-R | 150 | 135 | 4’ | |
3 | STA | 3μm ADS poly / Lub ADS | 150 | 135 | 3’ | |
4 | TFR | 1μm ADS poly / Lub ADS | 150 | 135 | 1’ |
Dans cette seconde gamme, la mise à niveau est réalisée à l’aide d’un I-Max R 54 μm à la place d’un papier abrasif. Ce support diamanté à liant résine, adapté pour le polissage des matériaux durs, permet de conserver une bonne planéité et de remplacer plusieurs centaines de papiers abrasifs.
La seconde étape est faite à l’aide d’un support MED-R. Ce support constitué de plots de résine sur lequel un ajout de suspension super abrasif pour MED-R est réalisé, permet de conserver une bonne planéité et a une durée de vie plus importante qu’un tissu de polissage.
Les étapes de finition sont faites avec la suspension ADS. Une suspension polycristalline concentrée LDP peut convenir parfois, si la fonte ne se corrode pas ou peu.
MICROSTRUCTURE
• Le réactif de Nital 4%
• Le réactif de Picra
• Le réactif de Le Chatelier
La liste est non exhaustive, les fontes ayant des structures proches de l’acier certains réactifs sont communs à ces deux matériaux. Les micrographies présentées ont été réalisées au moyen du logiciel PRESI VIEW :
=> Toutes les structures visibles sur les figures 17 à 22 ont été révélées à l’aide du réactif de Nital à 4%.
TÉLÉCHARGER LA LAB'NOTE
Remplissez simplement le formulaire ci-après :
Découvrez nos autres Lab’Note :
- Contrôle qualité impression 3D
- Contrôle traitement thermique
- Contrôle qualité dispositifs médicaux
- Contrôle qualité acier
- Contrôle qualité acier inoxydable
- Contrôle qualité fonte
- Contrôle qualité cuivre et alliages
- Contrôle qualité aluminium
- Contrôle qualité nickel
- Contrôle qualité titane
- Contrôle qualité matériaux céramiques
- Contrôle qualité électronique
- Contrôle qualité métaux précieux